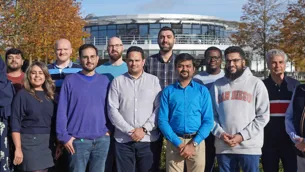
Academic team
Meet our academic team. Understand their reason for joining the Dyson Institute and their research interests.
Studying for an MEng at the Dyson Institute gives you the unique opportunity to study for your degree at the centre of a global leader in design innovation. You’ll learn engineering fundamentals from leading academics and put them into practice developing future Dyson products.
Twenty-first century engineering demands multidisciplinary experts. In your first two years you'll study a general engineering syllabus. Designed to be academically rigorous, and covering engineering fundamentals, theory is paired with real life learning as you rotate through many of Dyson's global engineering teams. You'll gain a strong academic and technical foundation across:
Building on these broad skillsets, in years three and four you'll choose to specialise in one of these areas. Whilst this can be challenging, we support you to find the specialism that best aligns with your skills and interests. With your unique skillset you'll have opportunities to develop your expertise and become an invaluable part of your team.
I believe opting for a degree programme with a work-based element has had the biggest impact on where I am in my career today. Without the workplace rotations in the first two years of the course, I wouldn’t have been aware of acoustics as an engineering discipline.
You'll learn and work on Dyson's Malmesbury campus, where you can make the most of our state-of-the-art facilities and enjoy in-person support from Dyson Institute academics and Dyson engineers. Working and collaborating with others, you'll help to solve problems that others ignore.
There are two academic semesters per year:
During term time, two days a week are devoted to lectures, revision, academic projects and self-study.
When you join, you will spend the remaining three days per week in an extended workplace induction, focused on technical training and development through problem-based learning, based on a real Dyson project. This will equip you with the skills and confidence to make a real impact when joining your first workplace rotation in January.
You'll have four workplace rotations across your first two years on programme, giving you an insight into mechanical, electronics and software engineering and New Product Innovation. In your third and fourth year, you'll have the opportunity to specialise in one of these areas, or combine through the electromechanical stream.
What happens in summer?
You will continue to spend three days per week in the workplace. On your two 'academic' days, you will continue your personal and professional development as outlined below:
The programme is taught across a variety of delivery methods to accommodate all styles of learning. These include lectures, tutorials, demonstrations, workshops, project supervision, group work and work-based learning.
The programme is assessed by approximately 40% examination and 60% assessed coursework. Both academic and workplace modules will contribute towards your degree qualification. Each year will be weighted accordingly to contribute to your final grade:
You'll receive a generous holiday entitlement of at least 40 days, plus eight bank holidays. This is a mixture of approximately ten days 'annual leave' which you can book any time (excluding study days), and 31 days 'academic leave', distributed at key points in the programme:
During the summer of year one you’ll take part in Summer Series – a programme designed to develop your understanding of end-to-end product development and collaborative working, that goes beyond your workplace experiences. Summer Series is an assessed module contributing to your degree qualification.
The Summer Series projects provide the perfect opportunity for first-year students to design, build and test creative solutions. It provides the students with the space to develop their professional skills on a project that they own and manage, putting into practice the theory and tools that they learn in the accompanying workshops. This hands-on approach is at the core of the Dyson Institute’s approach to learning and development and allows them to apply these skills in the other areas of the programme such as in the workplace.